There are a number of ways to create prototypes, although some are more efficient and effective than others.
To help you determine whether Prototype CNC machining is the best approach for your needs, here is a look at the perks and the pitfalls of this approach.
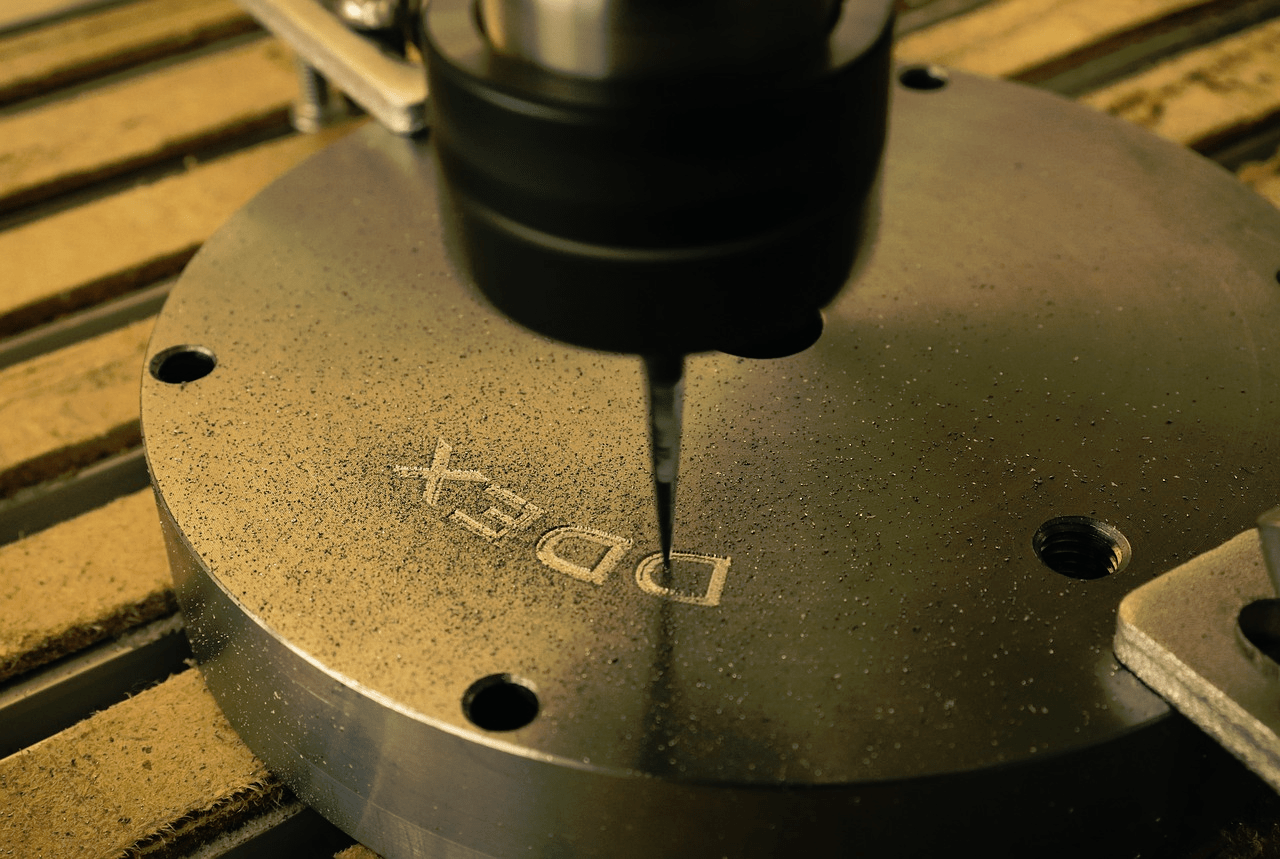
Form and function
Since additive manufacturing, otherwise known as 3D printing, became a mainstream technology it quickly became a popular option for rapid prototyping in a context when speed is of the essence.
This is all well and good for purely superficial prototyping purposes, but in reality the basic 3D printed models that are intended to stand in for the finished article early in the development cycle are aesthetically accurate but not practically applicable because of the materials involved.
Conversely with an affordable used CNC machine acquired from Revelation Machinery, functional prototype parts can be created rapidly, sharing exactly the same mechanical properties as the final design, so long as the materials being used mirror this as well.
Precision
Modern CNC machines can help to automate the prototyping process and thus create parts to a level of precision that would be almost impossible to replicate via manual means.
Engineers can conjure up the desired design in software, then send this file to the equipment and be certain that an accurate part will be produced according to their exacting specifications.
This precision also applies when changes to the design need to be made, no matter how minor. It is the work of a moment to go back and change some aspect which was found to be unsuitable in the first prototype, so that the follow-up is aligned more closely with what you are aiming to achieve.
Repeatability & sustainability
CNC machining is a sensible prototyping solution because equipment used to execute it can be put to work not only on making pre-production parts, but also to pump out the finalized components once the design team is happy with the results.
The repeatability that is afforded by such equipment goes hand in hand with sustainability. Human error will be eliminated from the equation so that there will be less waste of valuable materials, as well as a wider choice of potential materials in the first place. From aluminium and stainless steel to various plastics, a multitude of materials can be used for prototyping and full scale production alike.
Caveats & final thoughts
While CNC machining could be perfect for some prototyping scenarios, in others it might not. The considerations to keep in mind about this approach is that it is costlier than 3D printing and also generates more waste material because parts are machined from larger blocks. Furthermore there are machinery maintenance costs to keep in mind, although these can be controlled through correct use of equipment.
In terms of the limitations that machinery of this kind has from a technical level, there are certainly especially complex structures that simply cannot be replicated, meaning additive manufacturing may be the only option. And of course some pieces of equipment are more capable than others; such as 5-axis models being able to create trickier components than those with only 4. Of course if you are ultimately going to rely on CNC machining to produce the final part, then these limits will be relevant for prototyping anyway.
Finally it is worth noting that CNC machining can also be deployed not just to create components themselves, but also to fashion moulds that can then be used for prototyping through injection moulding.
In short, it makes sense to weigh up the advantages and issues of CNC machining against your own prototyping requirements to determine if this is the right path to take.